Author: Prof Pieter G Steyn, Principal- Cranefield College of Project and Programme Management
South Africa
Source: PM World Journal – Vol. I, Issue V – December 2012
www.pmworldjournal.net
Abstract
How to achieve sustainable supply chain performance has remained a complex challenge. Full commitment to process orientation and process management is required. Cultures of bureaucratic organisations do not allow for strategic supply chain
management, and the challenge is for them to transform to learning organisation paradigms and structures. The author advocates the effective utilisation of two crossfunctional supply chain structures, being customer-focused (on the demand side) and
capacity-focused (on the supply side), and a programme management system that includes a Balanced Scorecard for performance appraisal. In line with the conclusion of the Ohio State studies that leadership style effectiveness depends on situational factors, it is proposed that leaders should purposefully influence these factors by creating a supply chain configuration and culture conducive to learning and knowledge management. This will facilitate the successful application of a leadership style with high consideration and high initiating structure, which is essential. Moreover, it is critically important for organisations substantially to improve leadership acumen if they wish to achieve sustainable strategic supply chain success. Executives and supply chain managers have the added responsibility of acting as change agents for transforming the bureaucratic organisation to a learning entity.
The need for sustainable strategic supply chain management
Naslung and Williamson (2010) conclude that most people agree to the importance and potential benefits of supply chain management, but that it does not occur often enough in practice. Organisations struggle to evolve from theory to the successful
implementation of supply chain management. Mostly absent in practice are seamless chains, optimised flows, and networks of integrated organisations. These authors contend that, since the objective is to improve dynamic relationships, methodical
approaches to the implementation of supply chain management are needed, supported by sound empirically-based research to continue to develop the field. Designing, developing and managing cross-organisational processes are serious challenges when
one takes into consideration that most organisations are still struggling with internal process management. They go so far as to say that few, if any, examples exist of truly process-oriented organisations, yet process management is mentioned by prominent
researchers and practitioners as a prerequisite for successful supply chain management. These authors continue to express concern that the supply chain does not have clear roles or rules, measurement, and reward systems. They ask the question: “How can such a structure possibly be managed?”
Naslung and Williamson (2010) argue that systematic coordination of key processes for improved performance of the entire supply chain is fundamental to sustainable supply chain management. They assert that the discussion about collaboration and integration suggests that, for companies to proceed to a higher level, they first need to manage their internal processes properly before venturing into the cross-organisational level. The authors proceed to note the critical observation that companies need to commit fully to process orientation and process management in order to succeed with supply chain management. The current author believes that this is the core of the problem, which requires radical strategic transformation and change. Naslung and Williamson (2010) regard process orientation as important because an organisation’s value-adding capabilities depend on how well it manages its cross-functional processes. They support the views held by Hammer (2002) and Beretta (2002) that organisations should move away from the functional structure and functional goals if they wish to increase their customer focus and reduce the risk of sub-optimisation. The current author has also expressed this view (Steyn, 2001, 2003, June 2010, & July 2010). Moreover, Steyn (June 2010) distinguishes between “project-driven” and “non-project-driven” business models for supply chain management. He proposes a programme management approach similar to matrix project management to lead and manage cross-functional processes of the supply chain.
Lambert, Cooper and Pagh (1998) aver: “There is a great deal of confusion regarding what supply chain management involves. Many people using the term ‘supply chain management’ treat it as a synonym for logistics, or logistics that includes customers and suppliers. However, successful supply chain management requires cross-functional integration within the firm and across the network of firms that comprise the supply chain. The challenge is to determine how to successfully accomplish this integration.”
Kulkarni and Sharma (2004) argue that the vast majority of organisations that fail to apply supply chain management strategies to increase their agility will lose their status as preferred suppliers. They will be under enormous pressure to put in place a sound
supply chain management strategy and operations plan. According to Mangan, Lalwani and Butcher (2008): “The term, supply chain management (SCM), was originally introduced by consultants in the early 1980s and, since then, has received considerable
attention. The supply chain is a much wider, intercompany, boundary-spanning concept, than is the case with logistics.” The impression that ad hoc supply chain management is generally accepted or condoned emerges. In the current author’s opinion, an ad hoc approach to managing cross-functional processes in the supply chain is highly ineffective and inefficient. To motivate the assertion, one may refer to the adoption of matrix project management to coordinate and integrate activities productively in crossfunctionally structured project management processes.
Lambert et al (1998) identify eight cross-functional processes that constitute the activities of the supply chain. These are customer relationship management (CSM), customer service management (CSM), product development and commercialisation,
order fulfilment, returns, procurement, demand management and capacity planning, and manufacturing flow management. They further regard executive support, leadership excellence, commitment to change, and empowerment as key requirements for successful supply chain management, with information as a key enabler of supply chain integration. These authors assert that, due to the dynamic nature of the new economy, leadership and management should regularly monitor and evaluate the performance of the supply chain. They regard it as imperative that performance goals be met, and failing that, that supply chain alternatives be evaluated and change implemented. Lambert (2010), and Lambert and Schwieterman (2012), describe a comprehensive macro-level cross-functional view of CRM and CSM.
The current author (Steyn, 2001, 2003, June 2010, & July 2010) concurs with Lambert et al (1998) regarding the structuring of cross-functional supply chain processes, as also their opinions about leadership, commitment to change, and evaluating supply chain performance for the purpose of continuous improvement. However, the cultures of bureaucratic organisations do not allow for the abovementioned, and the challenge is for them to transform to learning organisation paradigms and structures. To be
successful, they are required to review how their supply chains are structured, led, managed and operated. Garvin (1993) offers the following definition of a learning organisation: “A learning organisation is an organisation skilled at creating, acquiring
and transferring knowledge and at modifying its behaviour to reflect new knowledge and insights.” He asserts that to stay competitive in the new economy, organisations must strive to move away from bureaucratic practices towards becoming learning
organisations that are far more agile and flexible. Responding to Murray-Webster and Thiry (2000), who propose three ways of shaping ross-functional project portfolios in organisations, the current author (see Figure 1) maintains that a supply chain cross-functional process portfolio should be added that could be project and/or operational in character and focused on improved internal and external customer service (Steyn, 2001, 2003 & July 2010). Steyn (June 2010) oncludes that the business model adopted by an individual organisation also plays a role. The business model can be project-driven, non-project-driven, or a hybrid of the two. Steyn (2001, 2003, June 2010 & July 2010) asserts that the best synergy will be achieved in the supply chain cross-functional process portfolio when a system of
programme management and review is utilised.
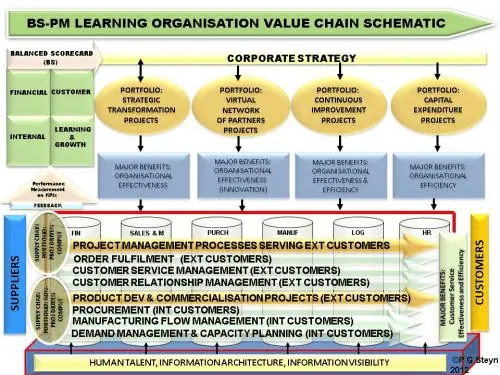
Cohen and Roussel (2005) contend that an innovative supply chain configuration driving the strategic objectives forward is of paramount importance. To derive the greatest benefit from the supply chain, one needs to consider five critical configuration
components: operations strategy, outsourcing strategy, channel strategy, customer service strategy, and asset network. They assert that next-generation supply chain strategies will not only support continuous improvements in productivity, but also drive
the achievement of business-level outcomes, with a strong focus on the customer. This supports the opinion that supply chain performance should be appraised and reviewed as advocated by Lambert et al (1998), Steyn (2001, 2003, June 2010, and July 2010), and others. Cohen and Roussel (2005) further state that it will be important in the future to identify objectives, which will include new revenue-generating services and time-tomarket, time-to-volume, and customer-segment-specific capabilities. They believe that the most successful roadmap implementations use a phased approach, which minimises risk and maximises the likelihood of success. The phases, in general, include detailed design, prototyping or proof-of-concept, a controlled pilot,
fine-tuning based on the results from the pilot, and full implementation. In agreement with the current author (Steyn, 2001, 2003, June 2010 & July 2010) these authors aver that a number of work streams are needed to support these phases, including
programme management, change management and value management.
According to Hines (2004), strategic fit has to be achieved between the supply chain strategies and the competitive strategies adopted by an organisation. Organisations must comprehensively understand customer needs by being customer-focused and
must recognise the key requirements in each target market segment they serve. Moreover, the same applies to the nature and structure of their supply chains and how they react under changing conditions in the market. Hugos and Thomas (2006)
conclude that the pace of change and the uncertainty about how markets will evolve has made it increasingly important for organisations to be aware of the supply chains in which they participate and to understand the roles that they play. This view supports Lambert et al (1998), who propose customer relationship management and customer service management as important cross-functional processes in the supply chain portfolio.
Sehgal (2009) argues, importantly, that the core functions of the supply chain relate to activities that are confined to the four walls of the corporation, and describes them as processes that are typically covered within what is called ‘the supply chain management space’. These are identified as demand planning, supply planning, manufacturing, warehousing, transportation, supply chain visibility, and supply chain network optimisation. Sehgal (2009) states that these functions generate data and transactions that can enable collaboration with partners, such partnering being typically beyond the scope of conventional SCM processes. The extended functions of the supply chain stretch the processes at either end of the corporate supply chain. These functions create the extended supply chain, representing the partners and enabling collaboration. Semolic (2010 & 2012) refers to this as a “virtual network of partners” and emphasises the vital importance of effectively and efficiently managing it as an important innovative component of the strategic supply chain. Concurring with Lambert et al (1998), Sehgal sees the demand end of the supply chain as customer relationship management (CRM), which complements the SCM core processes. Sehgal contends that the CRM process adds the capability for “quote and opportunity management, customer order and fulfilment management, returns and exchanges, customer collaboration, customer segmentation, profiling, and other customer analytics such as lifetime value and demographics”. The current author regards the demand side activities as “customer–focused”.
On the supply end, Sehgal (2009) sees supply chain planning as typically consisting of functions that produce a relatively longer-term picture for future operations. These processes are designed to provide decision-support tools for supply chain managers. The planning processes provide the ability to create multiple scenarios and evaluate them for specific metrics to determine the optimal plans. The output of these planning processes is adopted by the execution processes for action. Supply chain execution is seen as typically consisting of relatively short-term functions for immediate execution of operations. He believes that the supply chain execution processes are designed to create an implementation plan for the target business function such as shipping to stores, or production plans for a factory. They typically have a short execution scope, and may create multiple scenarios for identifying a realistic solution. The current author regards the supply side activities as “capacity-focused”. Sehgal (2009) sees collaboration
with partners engaged in the supply chain processes as essential. In agreement with Semolic (2010), he avers that demand and supply collaboration between partners allow the whole supply chain to react quickly to any demand changes and to capitalise on its ability to fulfil demand optimally. The current author concurs but further maintains that, to be successful, the planning and implementation actions need to be supported by a formal system of programme management and review.
A close analysis of the opinion of Lambert, Leuschner and Rogers (2008) is warranted. Originally proposed by Lambert et al (1998) as discussed earlier, they perceive SCM as the integration of eight key business processes across the supply chain. The
“procurement” process has been renamed “supplier relationship management” (SRM), which the current author regards as more appropriate. Their view is that these supply chain processes can link successfully if one manages relationships properly. For this to be successful, “management components” that provide guidance for implementation of each supply chain process must exist. They divide them into two groups: structural components and behavioural components. The current author agrees with the
conclusions of Lambert et al (2008) regarding the initiating structure and consideration dimensions of leadership behaviour, which they refer to as structural and behavioural “components”.
Their conclusions support the findings of the Ohio State studies on leadership (shown in Figure 2). The extensive research undertaken at Ohio State University identified a list of behaviours that were exhibited by leaders. The researchers finally concluded that there are only two independent dimensions of leadership behaviour, i.e. “consideration” and “initiating structure”. The “consideration” dimension involves primarily the leadership behaviour that is associated with creating mutual respect and trust, with a predominant focus on group member needs and desires. “Initiating structure” comprises the leadership behaviour that revolves mainly around organising and alleviating what group members should be doing in order to optimise productivity in an organised structural arrangement. These two dimensions yield four behaviour styles of leadership (as shown in Figure 2), and the hypothesis surfaced that the combination of high consideration and high structure would constitute the best style of leadership.
Figure 2: Four leadership styles derived from the Ohio State Studies
However, prolonged periods of testing delivered mixed results, leading researchers to conclude that practically there is no one best style. The argument arose that style effectiveness of a leader might depend on situational factors. Since style effectiveness
may depend on situational factors, the current author contends that leaders should purposefully influence these factors to render the organisation amenable to knowledge management and learning where a style of high consideration and initiating structure,
regarded best by the Ohio State studies, will succeed. This applies to strategic crossfunctional SCM. Hence, to be successful, executives must purposefully transform the organisation from a bureaucratic situation to a learning culture and system of
programme review, and must advocate a high consideration and initiating structure leadership style.
Based on statistically validated research done for a master’s degree, Shiraz Kola (2012) concludes that the company being investigated fails to strategically plan for change management, and its overall strategies do not consider the impact of change on its supply chain processes. He finds that the rate of transforming the organisation away from bureaucratic practises is not effectively and efficiently lead and managed, thereby compromising the supply chain performance, and compounding the risks the company faces in achieving its strategic goals and objectives. To counter the performance failure he recommends that the organisation transform its supply chain to a cross-functional, programme-driven portfolio based on a change management plan, and improve senior leadership. The current author supervised this research.
Lambert et al (2008) define the structural “components” as planning, control methods, knowledge management, workflow structure, organisation structure, and communication structure. They define the behavioural “components” as management methods, power and leadership, risk and reward, culture and attitude, and trust and commitment. They regard the behavioural “components” as less visible than the structural “components”, but essential for the successful implementation of the eight SCM processes. These authors sound a warning that often when managers try to implement business processes, they focus only on the structural “components”. They conclude that these efforts have a high failure rate because, even when the structure is sometimes acceptable, the right behaviours are not encouraged. The current author believes that this finding supports Garvin’s (1993) definition of a learning organisation, which clearly states that an organisation should “modify its behaviour to reflect new knowledge and insights”. Moreover, it supports the notion of applying strategic organisational transformation and change if sustainable SCM is desired.
In the current author’s opinion, this conclusion is strongly supported by the Harvey and Brown (2001) model for organisational performance and improvement, which links attitudes, beliefs, and values to behavioural strategy, and links organisational
architecture, design, and relationships to structural strategy. The fact that new behaviours are not encouraged entrenches bureaucracy, which then leads to supply chain performance failure because the organisation is unable to transform and change
to a knowledge-based learning entity. This again underscores Garvin’s (1993) argument that an organisation must become skilled at modifying its behaviour to reflect new knowledge and insights if it desires to eradicate bureaucracy, improve its performance
and stay competitive in the new economy. Upon analysing the above situational factors, the current author concludes that sustained competitiveness is not viable when primary emphasis is placed on structure while the leader demonstrates little consideration. This is even more pronouncedly unviable with the low initiating structure and consideration generally present in bureaucracies that are the causes of many operational failures. To quote one of the founding fathers of objective sociology, Emile Durkheim: “social life must be explained not by the conception of those who participate in it, but by the deep causes which lie outside of consciousness.” The author accordingly asserts that it is critically important for organisations substantially to improve their leadership talents and acumen if they wish to achieve sustainable strategic supply chain success. By implication this means that a situation needs to be created in the supply chain environment that requires a leadership style with high consideration and high initiating structure.
In a recent IBM study, entitled “IBM Global CEO Study: The Enterprise of the Future”, over 1000 CEOs from around the world were asked their opinions (IBM, 2008). The study found that CEOs are rapidly repositioning their businesses to capture growth
opportunities more effectively and efficiently. There is consensus amongst them that organisations are bombarded by change and that many are struggling to cope with the transformation. The gap between expected change and the ability to manage the
required transformation had almost tripled since IBM’s previous study in 2006. No longer are demanding customers viewed as a threat, but rather as an opportunity to differentiate. It should be added that the impact of the financial crisis that hit the global economy in the latter part of 2008 is accelerating the need for organisations to transform even more rapidly. The IBM (2008) finding is that all CEOs are adapting their business models, and at least two thirds are implementing extensive innovations, while
reconfiguring to take advantage of global integration opportunities.
The above development augurs well for the transformation of organisations towards a cross-functional strategic supply chain business model. In support of Cohen and Roussel (2005), the current author opines that supply chain business models are in dire
need of innovation and adaptation. It is not surprising that CRM as a cross-functional supply chain process has become very important in the enterprise of the future. Over time, the current author has observed that project and programme management
principles are becoming progressively more in demand in leading and managing the knowledge-based learning organisation value chain. Having a strong customer focus is an example of such a principle, and appropriate CRM achieves precisely that. It
continuously feeds customer needs back to the supply chain. As the current author has averred (Steyn, June 2010), when the supply chain portfolio is programme-managed, information is effectively and efficiently replicated throughout the entire value
chain via the supply chain structures.
This is a further example of a project and programme management principle being applied to the organisational value chain. Such replication is impossible to achieve in bureaucratic structures and paradigms. Moreover, the result of the IBM study indicates
that CEOs are moving aggressively towards global business designs, deeply changing capabilities, and partnering more extensively. The above research results have great significance for the programme approach to managing the modern supply chain, where leaders must provide considerable guidance on structuring tasks, while being highly considerate of employee needs and wants. The programme approach supports the opinion of Naslung and Williamson (2010), who argue that systematic coordination of key processes for improved performance of the entire supply chain is fundamental to sustainable supply chain management. It also supports their critical observation that companies need to commit fully to process orientation and process management in order to succeed with SCM.
Conclusion
The above research results have a ‘golden thread’, namely leadership and management acumen that connects them systemically. Leadership and management are two distinct but mutually supportive processes. Wheatley (1999) describes how revolutionary discoveries in chaos and complexity theory, quantum physics and biology are overturning existing models of science that have dominated for centuries. More than a decade on, it is even more obvious. The universe contains the polarities of chaos (change) and order (stability). Both dimensions form part of an entire spectrum of creativity. Each has the responsibility to ensure that tasks are effectively performed, whilst freeing up their natural strengths as well as engaging learnt behaviour and
knowledge. The modern organisational supply chain operates in a challenging environment characterised by change, but also requiring stability to deliver effective and efficient results. It is the responsibility of executive leadership to ensure that the
critical dimensions of consideration and initiating structure are institutionalised to achieve benefits of strategic importance from the supply chain operations strategy.
The prevalent ad hoc style of supply chain leadership and management employed by the vast majority of organisations is characterised by situational factors of chaos and instability. Formal programme structures supported by a cross-functional system of authority, responsibility and accountability are critically absent from these organisations. As discussed by Naslung and Williamson (2010), designing, developing and managing cross-organisational processes are serious challenges when one considers that most organisations are still struggling with internal process management. Referring to the four leadership styles derived from the Ohio State studies (as depicted in Figure 2), these organisations are operating their supply chains in bureaucratic paradigms where leaders fail to initiate cross-functional structures and generally demonstrate little consideration for employee needs and wants. A characteristic of cross-functional processes is the breadth of human resources that constitute the teams, sourced from various functional divisions and external suppliers (virtual network of partners). These resources are technical experts, and report to line managers. The line managers are their direct bosses, and have position power over them. Bureaucratic supply chain structures do not allow for designated process leaders and managers who operate in a cross-functional system of authority, responsibility and accountability.
In effectively leading, creating, implementing and improving in the context of supply chain activities, the current author has proposed a management philosophy and structure similar to matrix project management (Steyn, 2001, 2003, June 2010 & July
2010). Supply chain activities can best be orientated and focused on customer service excellence through a formal management system of programme review that includes a Balanced Scorecard, enabling performance appraisal and review. Moreover, it creates a situation conducive to high consideration and initiating structure leadership styles. Cross-functional supply chain process managers provide “what and when” guidance to the functional (and subcontracting) technical experts without having position power over them. Despite this, it is the unenviable task of these process managers to motivate the functional staff to deliver their best, and to be committed to the supply chain strategic outcomes. Such a situation requires unique leadership talents for successful coordination and integration of the cross-functional supply chain activities if synergy is to be achieved.
Since modern strategic SCM requires change to be managed while maintaining a high level of stability, persons appointed to positions of cross-functional process managers, programme managers, and the portfolio manager in charge of the supply chain, must possess superlative human skills. A situation must be created that calls for a leadership style at both the executive and supply chain levels of the organisation that provides substantial guidance about how tasks can be completed while being highly considerate of employees’ needs and wants. This means that executives and supply chain leaders have the added responsibility to act as change agents in transforming the organisation to a learning culture and ethos where a leadership style of high consideration and structure, regarded best by the Ohio State studies, will succeed.
The research findings clearly demonstrate the need to transform to a learning culture and cross-functional SCM. This combination will achieve effective and efficient customer focus and lead to sustainable competitive advantage. Organisations must
comprehensively understand customer needs and recognise the key requirements in each target segment that they serve. The supply chain character and structure, and reacting to changing conditions in the market, must be clearly understood, and CRM
plays a major role in informing leadership and management. Moreover, an innovative supply chain configuration and programme management model that drives the strategic objectives forward is of paramount importance. Cross-functional integration and
coordination across the network of partners that constitute the supply chain are critical to successful SCM.
Competent leaders, combined with a formal management system of programme review, readily allow for the structural dimensions of cross-functional organisation, authority, responsibility, accountability, workflow, efficient lines of communication, and knowledge management. The behavioural dimensions of trust, support, innovation, cohesion, autonomy, culture, attitude, commitment, and power, are also promoted. Moreover, a system of programme review as the current author has advocated (Steyn, June 2010) fully integrates and coordinates the eight cross-functional supply chain processes proposed by Lambert et al (2008), whereby synergy in the extended supply chain is established, enabling good relationships and collaboration between partners.
Recommendations
The major challenge for organisations is to implement a system of programme review as described above, and achieves the strategic supply chain benefits optimally for all stakeholders. The proposed system must include performance measurement. The
outputs of all cross-functional processes constituting the organisation’s supply chain must be measured, appraised and reviewed. Hence, key performance indicators (KPIs) must be allocated to each supply chain process, and linked to critical success factors
(CSFs) in a Balanced Scorecard strategy map, to enable performance management to become a reality. Resultant reviews will lead to continuous improvement initiatives that will further enhance the strategic performance of the supply chain. To be successful, it is imperative to create a situation conducive to a leadership style of high consideration and initiating structure for the system to operate in a knowledge-based learning culture, and to appoint such leaders.
The current author proposes a supply chain configuration consisting of two crossfunctional process components, being the “customer focus” structure and the “capacity focus” structure. . The customer-focused component contains the CRM, CSM, product development and commercialisation, and order-fulfilment/returns processes. The capacity-focused component contains the supplier relationship management (SRM), demand management and capacity planning, and manufacturing flow management processes. The exact configuration of the processes inside the two structural components depends on the business model adopted. It is imperative that process managers with excellent leadership skills be allocated to each process (or combination
of processes) in these structures. These process managers must then report to either a customer focus programme manager, or capacity focus programme manager.
When the size of the organisation warrants it, the programme managers would report to a supply chain portfolio manager who has the responsibility of keeping the executive informed. The cross-functional character of the proposed supply chain configuration
demands that the programme and portfolio managers command exceptional leadership skills. All managers in the cross-functional supply chain structure need to maintain high standards of human relations with the functional managers (and supplier partners) who provide them with the human resources responsible for executing the supply chain activities. The current author (Steyn, June 2010 & July 2010) has proposed that organisations appoint a chief portfolio officer (CPO) at the executive level, to whom the supply chain portfolio manager (and other portfolio managers) must report, and that they shape their cross-functional supply chain processes into programmes in accordance with their adopted business models. Business models can vary from nonproject-driven, to project-driven, or a hybrid of the two. A non-project-driven business model generates revenue by selling products and services to external customers, while a project-driven business model generates revenue by undertaking projects for external customers. Their supply chain configurations also differ. Supply chain configurations differ according to the size and business model of the organisation, with process managers reporting to one or more programme managers. In large organisations, a process manager might head each of the supply chain processes. Figures 3 and 4 illustrate the basic concepts. Supply chain processes may be grouped in smaller organisations. Each group would then be allocated a process manager. However, it is imperative that organisations first adopt a learning culture and structure if they wish to achieve sustainable strategic supply chain success.
Figure 3 illustrates the cross-functional supply chain programme management structure for an organisation adopting a project-driven business model. Project-driven organisations are unique. To win orders, they bid on RFPs (requests for proposals)
received from the external customers. When successful in their bids, they generate income (revenue) by executing the projects. For effective and efficient customer service, many utilise cross-functional (matrix) project management processes that constitute the project-driven component of the supply chain portfolio. Uniquely, the order fulfilment, and product development and commercialisation supply chain activities become part and parcel of the cross-functional project management process activities performed by the project team members. Moreover, there are no returns, only a possibility of failed projects. The customer focus structure comprises the abovementioned cross-functional project management processes that absorb order fulfilment and product development activities, as also the CRM and CSM processes. The three remaining supply chain processes constituting the capacity focus structure are SRM, demand management and capacity planning, and, lastly, manufacturing flow management. The capacity focus structure supports the cross-functional processes in the customer focus structure of the supply chain.
Figure 3: The supply chain programme management structure for a project-driven business model
Figure 4 (below) illustrates the cross-functional supply chain programme management structure for an organisation adopting a non-project-driven business model. The customer focus structure again includes CRM and CSM, but in addition also comprises
separate order fulfilment/returns, and product development and commercialisation processes. The product development and commercialisation process is unique in the sense that it is the only cross-functional supply chain process in the non-project-driven business model that is project-managed. The three remaining supply chain processes constituting the capacity focus structure are again SRM, demand management and capacity planning, and, lastly, manufacturing flow management. The capacity focus structure supports the cross-functional processes in the customer focus structure of the supply chain.
Figure 4: The supply chain programme management structure for a non-project-driven business model
Summary
The research indicates that most organisations agree regarding the importance and potential benefits of SCM, but struggle to evolve from theory to successful implementation. Successfully managing cross-organisational processes as required by the modern supply chain approach, is a serious challenge, especially when one considers that most still struggle with internal process management. Consequently, organisations need to manage their internal processes properly before venturing into
the cross-organisational level. Full commitment to process orientation and process management is required in order to achieve sustainable SCM. The core functions of the supply chain relate to activities that are confined to the internal environment of the
organisation. The extended functions of the supply chain stretch the processes at either end of the supply chain, representing a virtual network of partners. Demand and supply collaboration between partners demands that the whole supply chain react quickly to any demand changes and that it capitalise on its ability to fulfil demand optimally. Researchers and practitioners agree that organisations that fail to increase their flexibility and agility will lose their status as preferred suppliers.
When managers attempt to implement business processes, they have a tendency to focus only on structure. Several authors report that these efforts have a high failure rate because the right behaviours are not encouraged. If organisations wish to increase their flexibility, agility and customer focus, and simultaneously reduce the risk of suboptimisation, they need to move away from the functional structure and functional goals.This demands initiating a cross-functional supply chain structure and programme management system that includes a Balanced Scorecard for performance appraisal. The programme management system fully integrates and coordinates the crossfunctional processes, and brings synergy to the extended supply chain, enabling good relationships and collaboration between partners. Cultures of bureaucratic organisations do not allow for strategic supply
chain management, and the challenge is for them to transform to learning organisation paradigms and structures.
Style effectiveness of leaders depends on situational factors, and leaders should purposefully influence these factors to create an organisational culture of learning and knowledge management where a high consideration and high initiating structure leadership style will succeed. This includes the supply chain environment where a leadership style with high consideration and high initiating structure is of paramount importance. Moreover, it is critically important for organisations substantially to improve leadership acumen if they wish to achieve sustainable strategic supply chain success. The research findings clearly demonstrate the patent need to transform to a learning culture and cross-functional SCM. Executives and supply chain managers have the added responsibility of acting as change agents for transforming the bureaucratic organisation to a learning entity.
BIBLIOGRAPHY:
Beretta S, 2002, “Unleashing the Integration Potential of ERP Systems”, Business Process
Management Journal, 8, (3).
Cohen S, and Roussel J, 2005, “Strategic Supply Chain Management: The Five Disciplines for
Top Performance”, New York: McGraw-Hill Professional.
Garvin D A, 1993, “Building a Learning Organization”, Harvard Business Review, July-Aug.
Harvey D, and Brown D R, 2001, “An Experiential Approach to Organisation Development”, 6th
Edition, Prentice Hall Business Publishing.
Hammer M, 2002, “Process Management and the Future of Six Sigma”, Sloan Management
Review, 43, (2).
Hines T 2004, “Supply Chain Strategies: Customer Driven and Customer Focused”, London,
Elsevier.
Hugos M, and Thomas C, 2006, “Supply Chain Management in the Retail Industry”, San
Francisco: John Wiley and Sons.
IBM Corporation, December 2008, “IBM Global CEO Study: The Enterprise of the Future”.
Kulkarni S, and Sharma A, 2004, “Supply Chain Management Creating Linkages for Faster
Business Turnaround”, New Delhi: Tata McGraw-Hill Publishing Company Limited.
Kola S, 2012, “The Importance of Change Management in Introducing a Re-engineered
Business Process for Railway Operations”, unpublished Masters Dissertation, Cranefield
College of Project and Programme Management, South Africa.
Lambert D, 2010, “Customer Relationship Management as a Business Process”, Journal of
Business and Industrial Marketing, Volume 25, No1.
Lambert D, Cooper M, and Pagh J, 1998, “Supply Chain Management Implementation Issues
and Research Opportunities”, The International Journal of Logistics Management, 11, (1).
Lambert D, Leuschner R, and Rogers D, 2008, “Supply chain Management: Processes,
Partnerships, Performance”, 3rd Edition, Edited by Douglas Lambert. Columbus: Supply Chain
Management Institute.
Lambert D, and Schwieterman A, 2012, “Supplier Relationship Management as a Macro
Business Process”, Supply Chain Management: An International Journal, Vol 17, No 3.
Mangan J, Lalwani C, and Butcher T, 2008, “Global Logistics and Supply Chain Management”,
San Francisco: John Wiley and Sons.
Murray-Webster R, and Thiry M 2000, “Gower Handbook of Project Management”, 3rd Edition,
Chapter 3, “Managing Programmes of Projects”, Gower publishing, England, Ed. Rodney Turner.
Naslund D, and Williamson S, 2010, “What is Management in Supply Chain Management? – A
Critical Review of Definitions, Frameworks and Terminology”, Journal of Management Policy
and Practice Vol. 11 (4).
Sehgal V, 2009, “Enterprise Supply Chain Management: Integrating Best in Class Processes”,
San Francisco: John Wiley and Sons.
Semolic B, 2012, “For top Performance, Modern Organisations require Sustainable Innovation
Systems”, Proceedings of the IPMA Research Expert Seminar,Riversdale, Western Cape,
South Africa, March.
Semolic B, 2010, “Virtual Networks of Partners”, Proceedings of the IPMA Research Expert
Seminar, Cape Town, South Africa, March.
Steyn P G, 2010, “The Need for a Chief Portfolio Officer (CPO) in Organisations”, PM World
Today, July, Vol XII, Issue VII.
Steyn, P G, 2010, “Programme Managing The Supply Chain Portfolio”, PM World Today, June,
Vol XII, Issue VI.
Steyn P G, 2003, “The Balanced Scorecard Programme Management System”, Proceedings
of the 17th IPMA Global Congress on Project Management, Berlin, Germany.
Steyn P G, 2001, “Managing Organisations through Projects and Programmes: The Modern
General Management Approach”, Management Today, Vol 17, No 3, April.
Steyn P G, and Schmikl E, 2010, “Programme Managing Organisational Transformation,
Change and Performance Improvement”, Cranefield College of Project and Programme
Management.
Wheatley M J, 1999, “Leadership and the New Science. Discovering Order in a Chaotic World”,
Berrett-Koehler Publishers.
Prof. Dr. Pieter Steyn
Founder, Head Director, Principal, Professor
Cranefield College of Project and Programme Management
Johannesburg & Western Cape, South Africa
cranefield2@cranefield.ac.za.
Dr. Pieter Steyn is Founder and Principal of Cranefield College of Project and Programme Management, a South African Council on Higher Education / Dept of Education accredited and registered Private Higher Education Institution offering an Advanced Diploma, Postgraduate Diploma and Master’s Degree in project and programme-based leadership and management. Professor Steyn holds an engineering degree (BSc Eng), MBA and Doctorate in business management and is a registered Professional Engineer. Dr. Steyn founded consulting engineering firm Steyn & Van Rensburg (SVR) in 1970. (Projects included First National Bank Head Office (Bank City), Standard Bank Head Office, Mandela Square (all in Johannesburg), Game City and The Wheel Shopping Centres (Durban)). He was appointed professor in the Department of Management, University of South Africa (1976), was Founder Chairperson (1977) of the Production Management Institute of South Africa, and helped pioneer Project Management as a university subject at the post-graduate level in 1979 at the University of South Africa. He was professor of Project and Operations Management at the TUKS Graduate School of Management, University of Pretoria from 1990 until retiring in 1998. Pieter was Chairperson of the Commission of Enquiry into the Swaziland Civil Service in 1993; Project Leader of the Strategic Management Team for the Gauteng Government’s Welfare Department and Corporate Core, 1994 to 1996. He founded the Cranefield College of Project and Programme Management in 1998. Pieter is co-author of the “International Handbook of Production and Operations Management,” (Cassell, London, 1989, ed. Ray Wild) and author of many articles and papers on leadership and management.
Pieter is a founder Fellow of the Production Management Institute of South Africa, and a member of the Association of Business Leadership, Industrial Engineering Institute, Engineering Association of South Africa and Project Management South Africa (PMSA). He is founder and past President of the Association of Project Management, South Africa (APMSA) and South Africa’s former representative on the Council of Delegates of the International Project Management Association (IPMA), 2000-2005. He is currently a member of IPMA’s Research Management Board (since 2007). Pieter is also Director of the De Doornkraal Wine Estate in Riversdale, Western Cape.